自分が今飲んでいるサプリメントはどうやって作られているのか。本当に安全なのか。 サプリメントを利用したことがある人なら一度は気になったことがあるのではないだろうか。今回はその問いに応えるべく、ファンケルのサプリメント製造についてレポートする。前回に続き、ファンケル主催の「サプリメント安心・安全セミナー」に参加し、静岡県三島市にある工場を見学してきた。
ファンケルのサプリメント基幹工場、三島工場のスペック
ファンケルの化粧品やサプリメント、発芽米は現在、国内6か所の工場で製造されている。サプリメント製造は1994年から横浜工場で生産をスタートし、増産や商品ラインアップが増えたことに伴って2016年に2拠点目となる千葉工場が開業。その後もサプリメント売上高は伸び続け、2015年~2019年度の5年間で1.5倍にも成長した。2019年度の売上高は440億円にも達した。
サプリメント事業の成長・拡大の理由としては、国内での流通チャネルを展開強化したこと(通信販売のほか直掩店舗販売、卸売も開始)に加えて、中国での越境ECを始めとするグローバルでの展開を強化してきたことがある。
これを受けて、ファンケルではさらなる生産能力の増強が急務となった。また、急激な需要変動に対応するためには、自社工場での内製化率をアップさせる必要がある。そこで、ファンケルは2021年、第3の生産拠点として静岡県三島市にサプリメント専用工場として竣工した。
三島工場の管理充填グループ課長の大沼宏輔氏が、工場のスペックについて説明する。
「三島工場は竣工当初からサプリメントの基幹工場として設立され、ファンケルグループ最大の延床面積(30,715㎡)を誇ります。投資額も工場施設としてはグループ最大の80億円です。
5階建の建物のうち、工場として稼働しているのが1階および2階の半分。2階の残り半分と3階は将来の増産に備えた未実装スペースとなっています。5階が品質管理エリアおよび事務会議スペースです。
1日あたりの生産能力は、サプリメントが1日最大1085万粒、重さにして3.1トン。アルミ袋製品では1日最大6万袋を生産できます。また、当社の特徴的な技術で、多種類のサプリメントを1パックに詰め合わせる“分包”という技術があるのですが、これは1日最大約25万包を生産可能です。」
2024年6月現在、三島工場では完成品目で47品目を製造しており、バルク数は23品目。バルクとはサプリメントの中身のことで、錠剤型とハードカプセル型がある。
ちなみに、三島工場では自社製品以外にキリンHDの製品15品目も生産している。
医薬品レベルの品質・安全基準GMPをクリア
ファンケルのサプリメントは、徹底した品質管理体制のもと製造されている。その基準の1つがGMP(Good Manufacturing Practice)だ。工場長の小島 俊介氏が解説する。
「GMPとは、サプリメント先進国アメリカ発祥の『製品の品質と安全性の確保』を目的とした製造認可基準です。原料の入荷から製品の出荷までの過程において、製品が安全で一定の品質を保たれるように定められたシステムで、日本では医薬品に対して法的拘束力があります。これをクリアしていない医薬品は国内では販売できません。
サプリメントについては第3者認定制度であり法的拘束力はありませんが、当社では直接口にするものだからこそ医薬品と同等レベルを目指したいとの思いから、2005年に大手メーカーの横浜工場が自社工場では初の『健康補助食品GMP』を取得しました。ファンケルの全工場で生産される全製品に対してこの基準を遵守し続けています。」
さらに、FSSC22000 (Food Safety System Certification 22000)という食品安全のための国際規格(第3者認定制度)も、あえて自社で課している。その理由について、小島氏は次のように話す。
「GMPがモノづくりの生産工程全般のシステム化に重点を置いているのに対し、FSSC22000は食品づくりの安全マネジメントをより強固にしたものです。たとえば、衛生管理や異物混入、フードディフェンスに関する危害因子の分析など、詳細のシステム化を求められます。GMPとFSSC22000を2重に課すことで、より高いレベルの品質・安全性が達成できるものと考えます。」
工場見学①原料の入荷~保管~搬出
では、実際にファンケルのサプリメントがどのように製造されているのか、その製造現場を追ってみたい。
まずは工場の1階から。1階には入出荷倉庫エリアと製造エリアがある。原料の入荷から保管、搬出までの流れを、購買グループ課長の小原勇気氏が説明する。
「まず、サプリメントの原料となる資材は、1階の入荷入出荷用の入口で業者から受け取り、発注データと実物との照合を経て、倉庫へと搬入します。一度に倉庫で保管できるパレット数は240枚台。倉庫内は24時間空調管理を行い、出入口でいりぐちはダブルシャッターを採用しています。そのため、倉庫が外と繋がることはありません。
倉庫内では自動で動く無人運転フォークリフトが稼働しており、管理システム上に登録されたデータに従って、パレットを必要な場所に格納していきます。搬出する際もフォークリフトが目的のパレットを抜き取り、仮置き場に移動してくれるので、重い荷物を人力で積み下ろしする労力が大幅に削減でき、省人化に役立っています。」
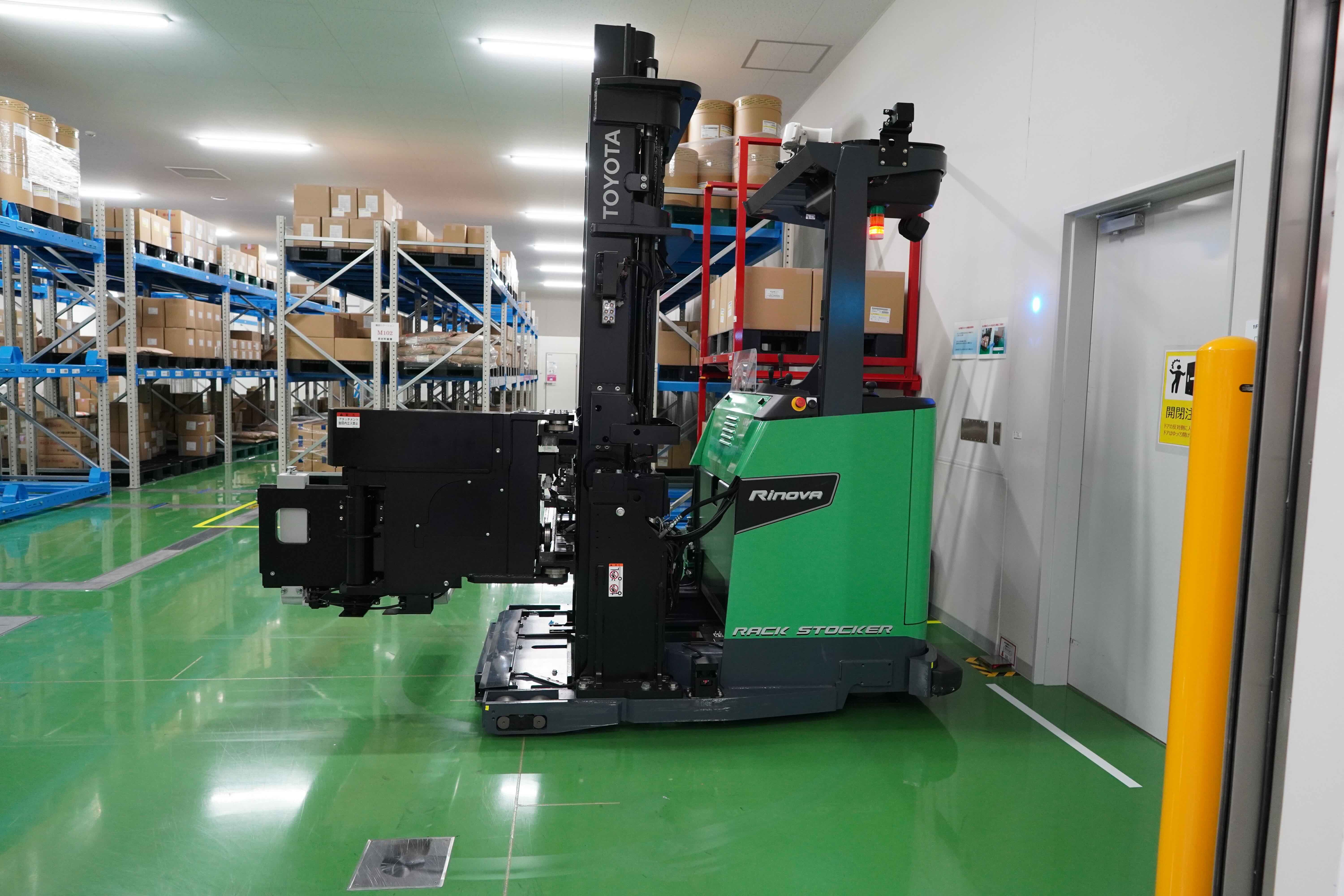
製造エリアへの搬入する出の際は、原料資材の入った段ボールにエアシャワーを浴びせ、外装に付いた微細な粉塵異物を吹き飛ばす。きれいな状態になった原料箱を製造エリアの担当者が受け取り、製造エリア内へと運ぶことで、異物混入を防いでいる。
工場見学②バルクの製造~充填
1階の製造エリアは、入出荷倉庫エリアとは壁を隔て、完全なクリーンルームとなっている。その清浄度はクラス100,000という、製薬や食肉加工に求められる高いレベルだ。
製造エリアへの入口には、生体認証を導入し、エリア内の至る所にカメラを設置して、不審者は絶対に入れない仕組みになっている。また、専用更衣の着用および持ち込み物も厳重に管理し、意図的な異物混入を防いでいる。
サプリメントが原料から製品になるまでの工程は、下図の通り。
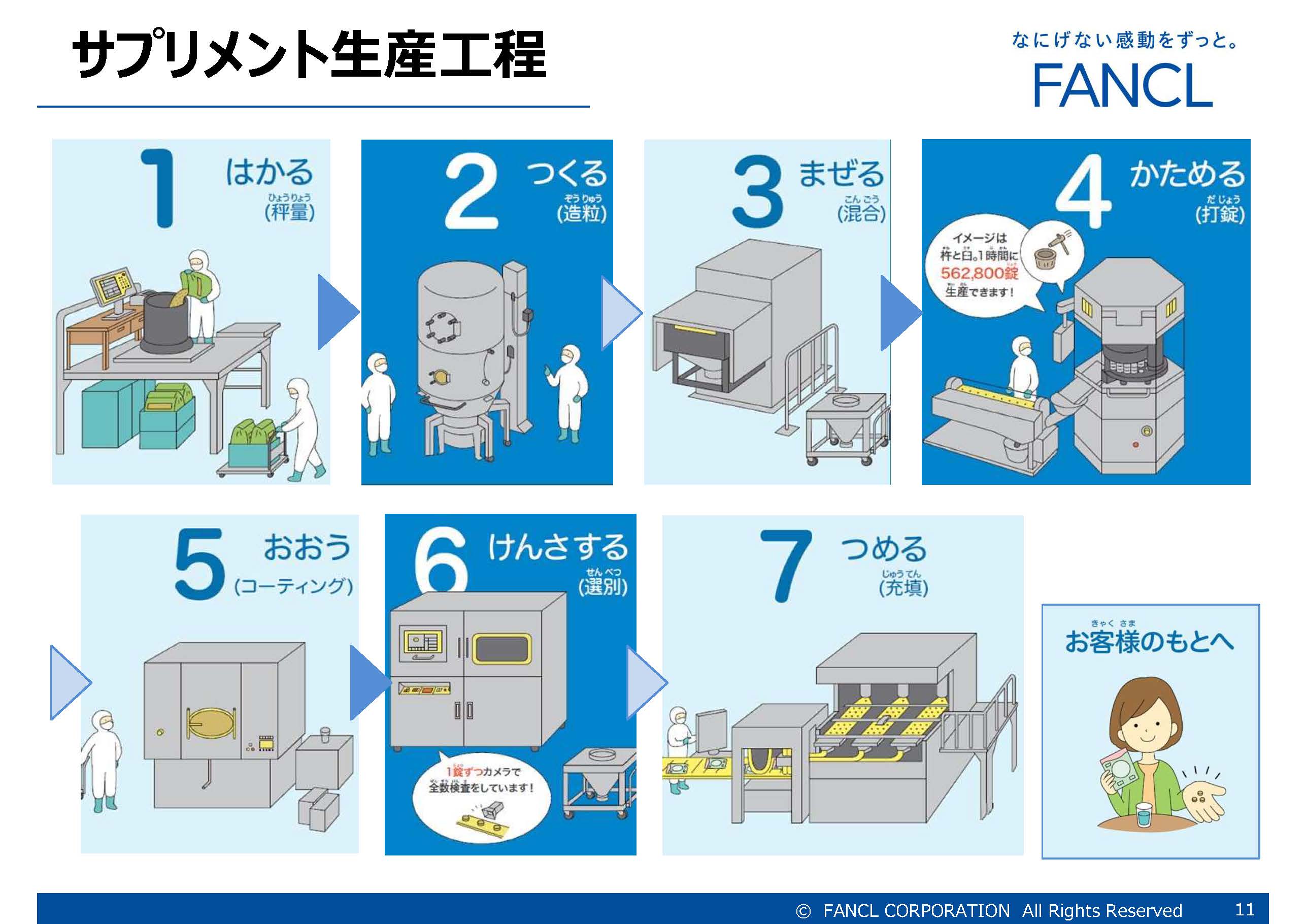
工程間を移動する際、中間原料やバルクなどは移動式専用タンクに入れられ、キャスターで運ばれる。専用タンクは約500㎏~約1tにもなるが、このキャスターのおかげで女性一人でも安全かつスムーズに動かすことが可能だ。
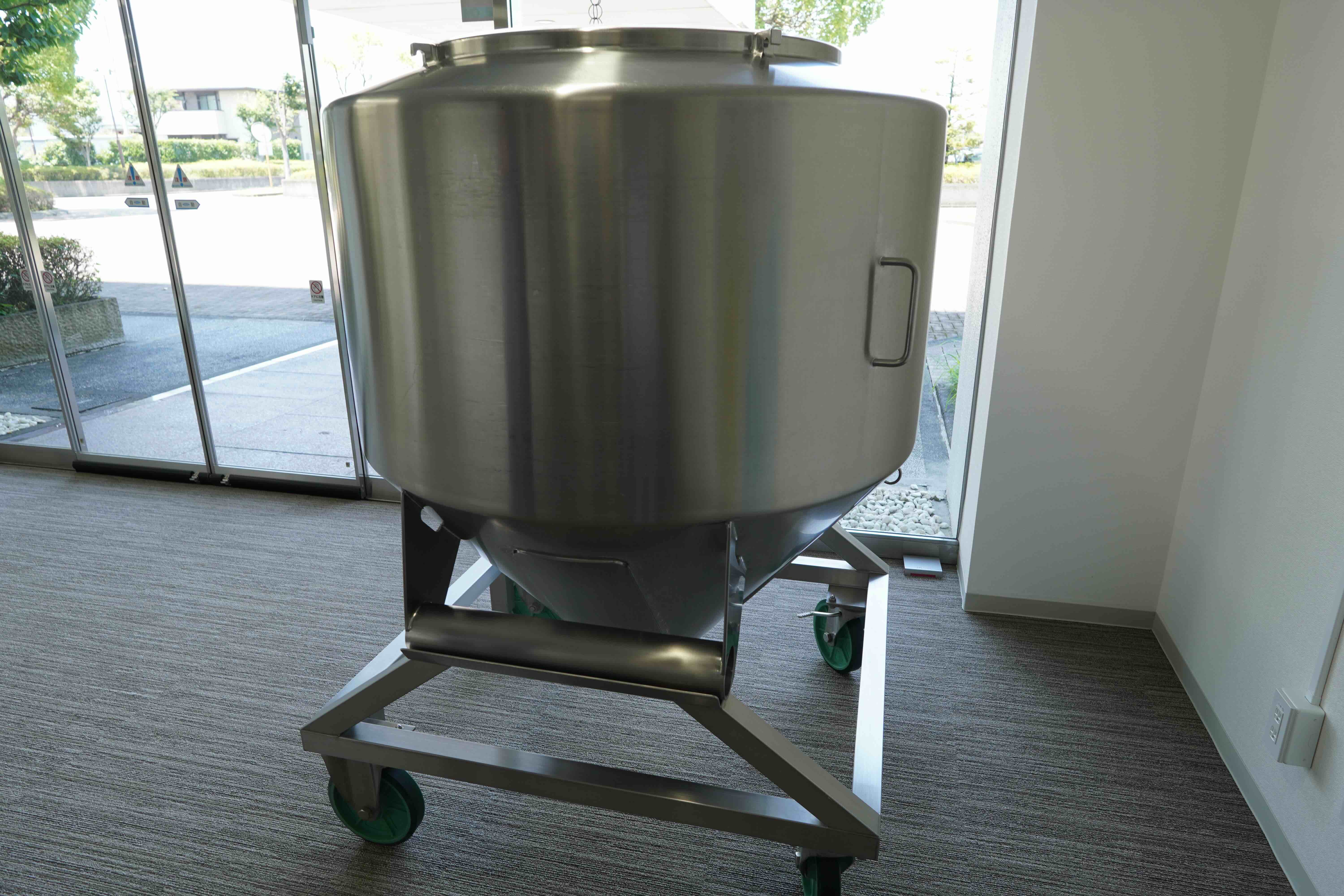
タンクは天井まで持ち上げられ、造粒機の上にセットされて、中身が機械の中に投入される仕組みになっている。小島工場長は次のように話す。
「このような仕組みにすることで、中身に一切手を触れることなく移動ができます。サプリメントの衛生管理では人が触れることが一番の汚染源になるので、〝製造工程で一度も手を触れない“というのが非常に重要なのです。」
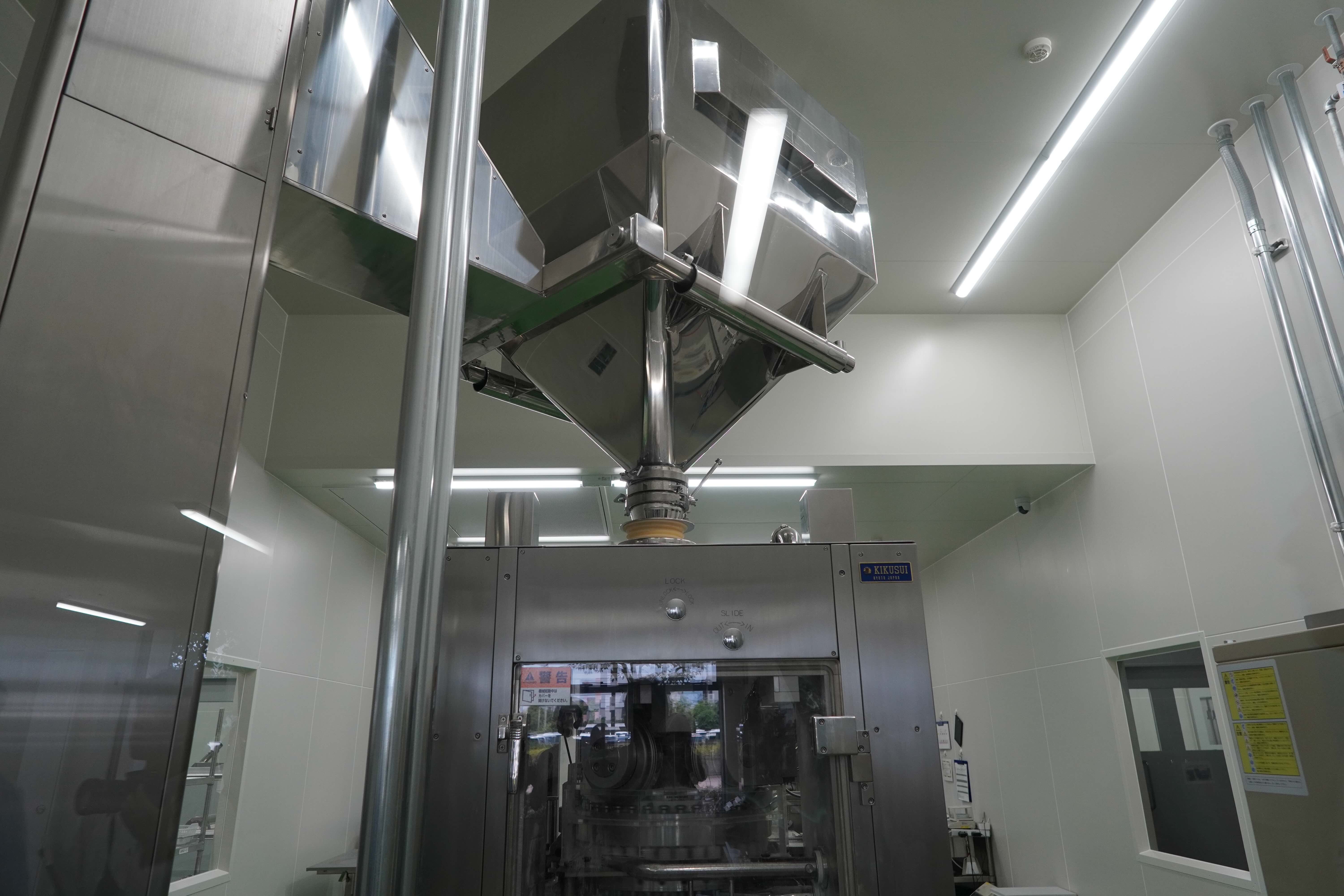
三島工場の特長として、最新の製造機械が導入されている点があると、小島氏は説明を続ける。
「粉末を圧し固めて錠剤にする打錠機は、自動運転も可能で、夜間でも製造することができます。不具合があればエラーで教えてくれますし、万一、バルクの重さや形状に小さなずれが生じた場合でも、自動的にフィードバックして正しく調整する機能を備えているので、人が終始見守っている必要がありません。」
見学の際、2台ある打錠機のうち1台が清掃中で停止していた。小島氏によると、この清掃作業が最も人手と時間がかかり、神経も使うそうだ。なぜなら、サプリメントの成分に含まれるアレルギー物質が少しでも残存していると、次に別の種類のサプリメントを打錠する際、その成分が混入してしまうおそれがあるためだ。ほんのわずかな混入でも、健康被害に繋がりかねない。だから、半日~1日かけて徹底的に洗浄するのだという。
打錠機以外にも最新式の機械は多くある。たとえば、サプリメントに不良品がないかを検査する錠剤選別機は、1分間に40万錠の高速検査が可能。6台のカメラで全方位から撮影をし、異常がないかを確認をしている。
2階に移動すると、高速分包機がある。この機械は、ファンケルがメーカー3社と共同開発をしたオリジナルで、1分間に200包を包装できる。
「一般的な分包機の約4倍速で生産できます。当社のこだわりが詰まった機械です」と小島氏は胸を張る。
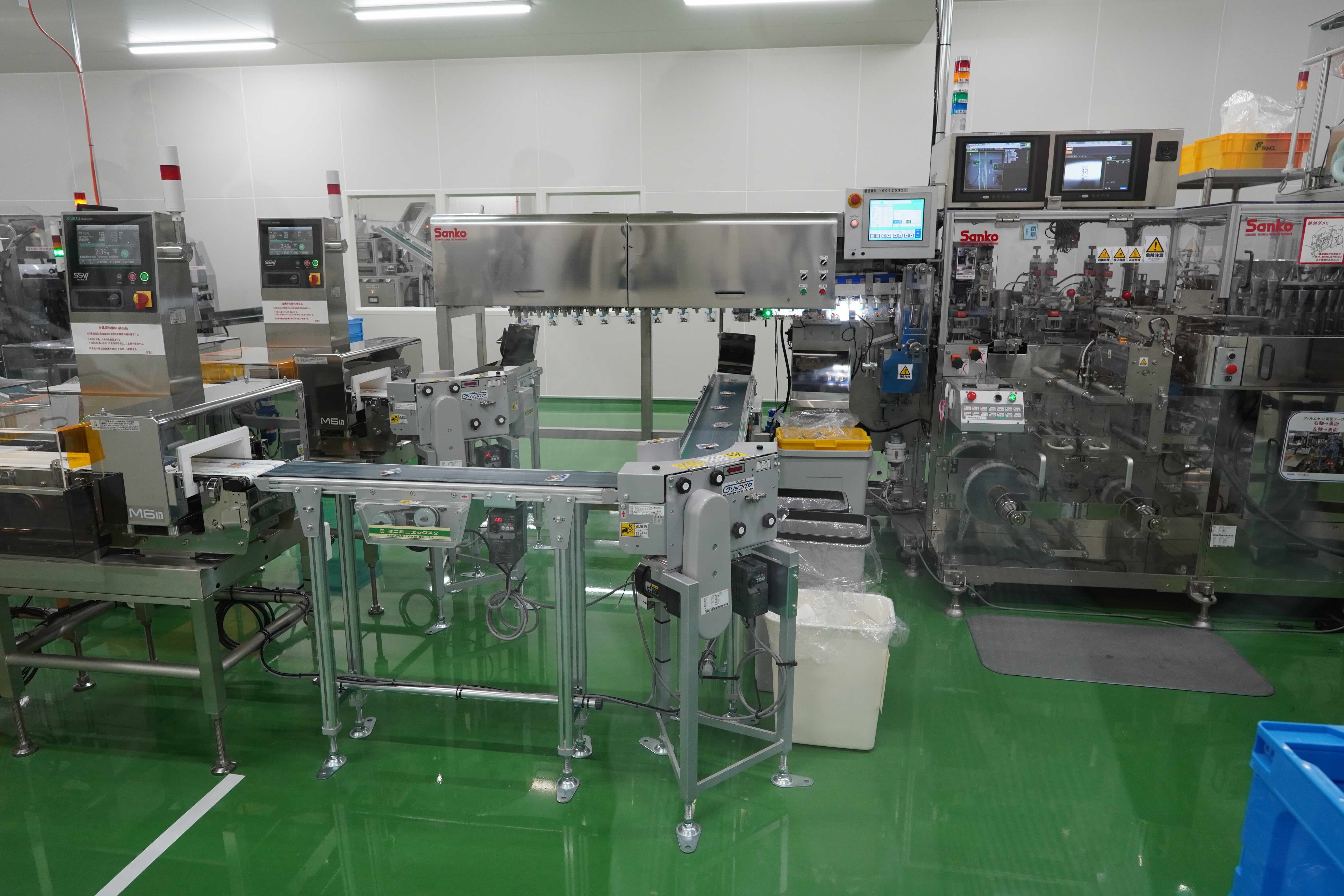
工場見学③品質管理
5階には「品質管理室」があり、ここで徹底した原料および製品の品質管理が行われている。
まず1つめの検査は、原料および製品の製造ロットごとの検査だ。使用する原材料については、検査で合格となったもののみ使用する。また、各製造工程でも都度、検査による品質評価を行っており、合格になったものしか次の工程に進むことができない。
2つめの検査として、製造委託先工場の管理がある。委託先で生産した製品に関しても自社工場と同じ品質が提供できるよう、定期的に委託先工場に出向いて監査を実施している。
品質管理グループ課長の田村 佳子氏が説明する。
「原料の受け入れ検査については、FT-IRという分析機で成分測定を行います。モニターに映し出される検査品の波形と標準品の波形を比較し、一致すれば問題なし。不一致であれば、別の原料だと判定できます。そのようにしてすべての原料のロットを調べ、原料が間違って納品されていないか、他の成分が混入してないかなどを検査しています。もちろん機械任せではなく、人間の五感を使って、色や匂いにおかしいところはないかもチェックしています。
製品については外観や性状、割れにくさ、溶けやすさ、微生物を含めた異物混入がないか、使用感に問題はないか、パッケージの印刷や密閉性に問題がないかなどを測定機と人の五感で検査しています。」
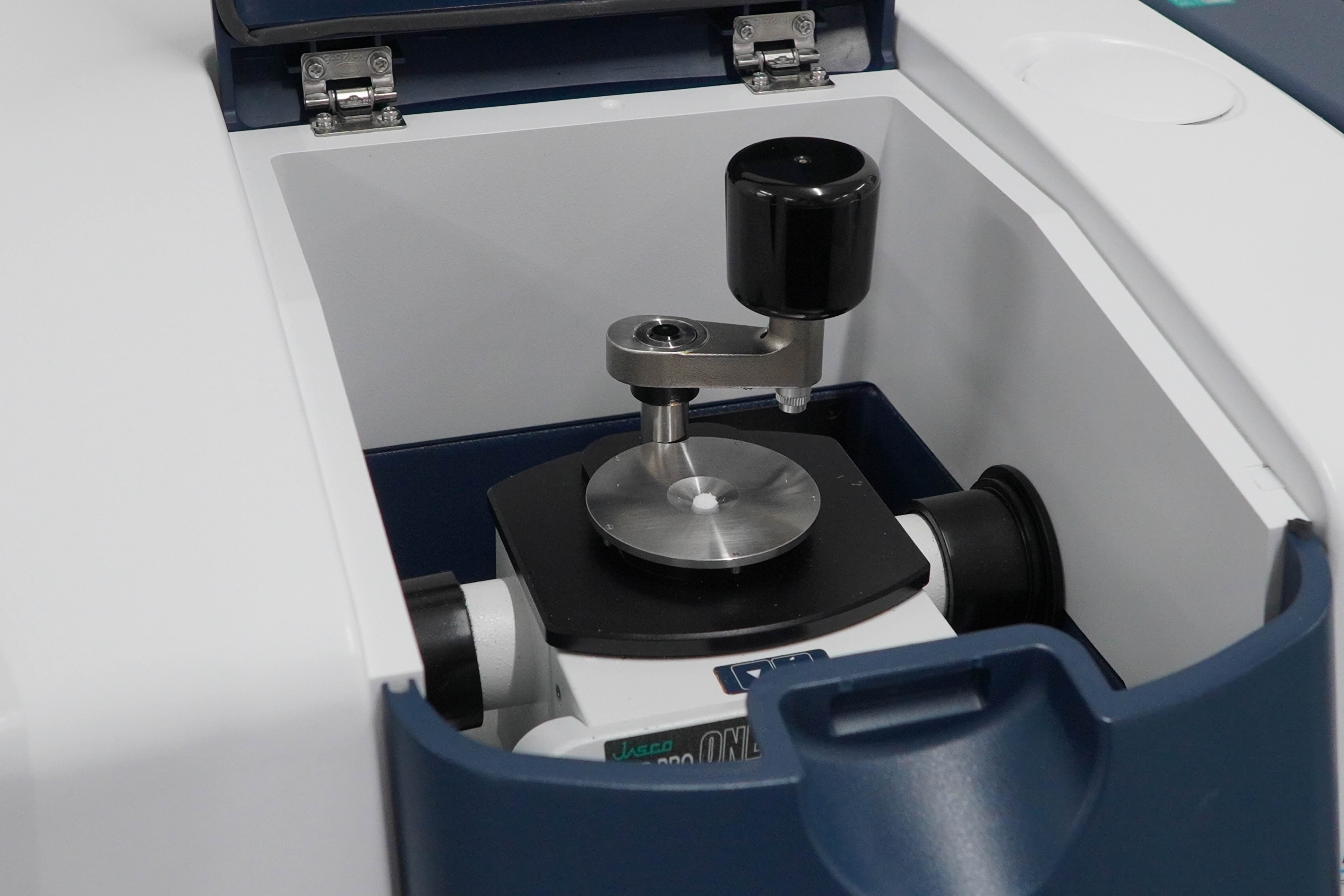
万が一、検査でエラーが見つかった場合、社内の品質管理の運用システムに則ることでを見直し、原因の調査や再発防止などの対策が速やかに行われることになる。
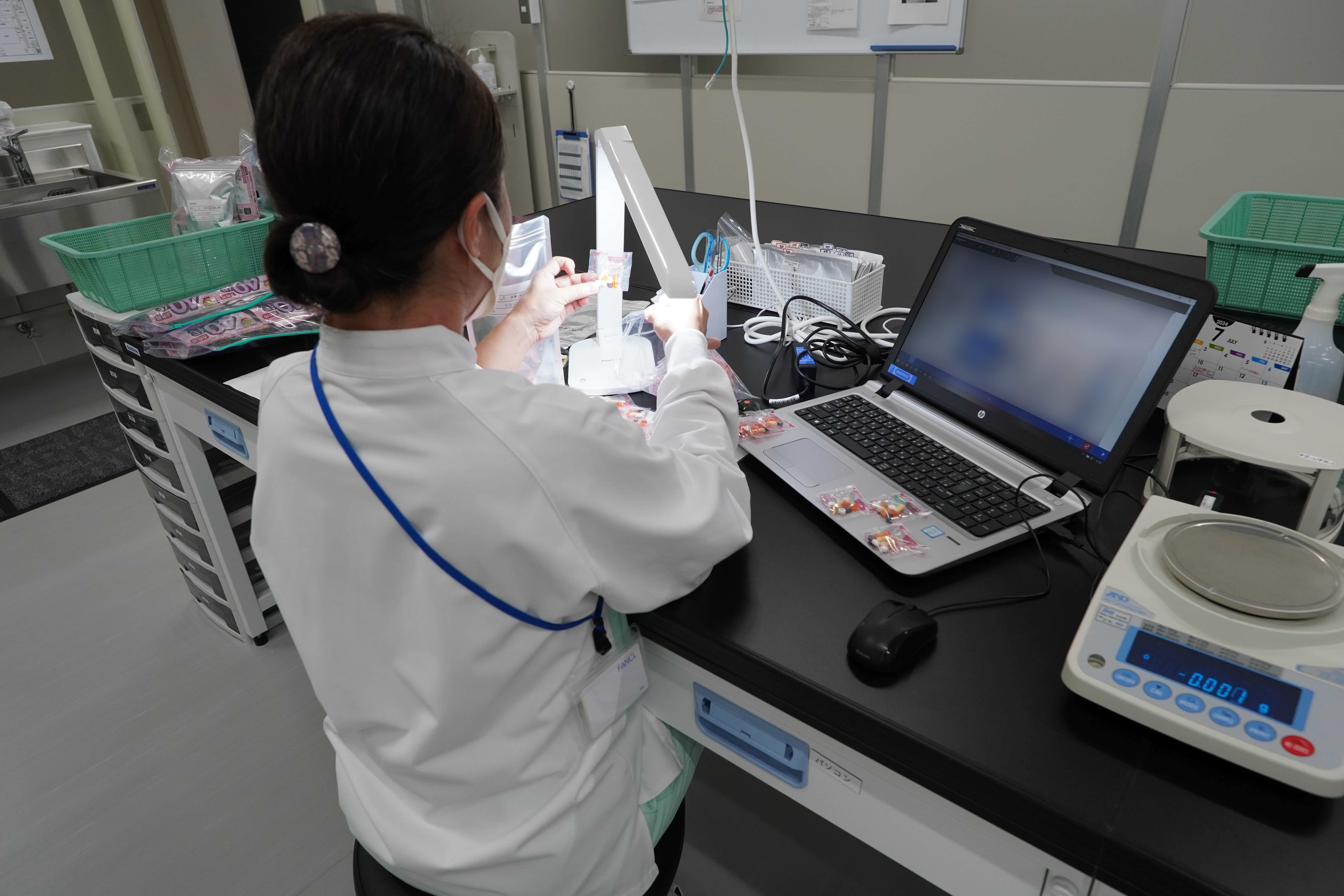
良い商品は良い人から 工場の全従業員で取り組むGMP教育
高い品質や安全性を保証していくには、従業員の意識を高める教育が欠かせない。三島工場では、派遣社員やパート職員も含む全従業員でGMP教育に励んでいると田村氏は話す。
「月1回、GMP研修を実施しています。同じ内容の講座を3回行うことで、全従業員がもれなく参加できるように工夫しています。
私たちが大切にしている品質管理の考え方は、起きたことの是正は当然として、これから発生するかもしれない事故やエラーをいかに未然に防止していくかです。そのために、従業員たちで10名ほどの小集団をつくり、3カ月で1つの課題をクリアしていく取り組みをしています。三島工場には10チームあるので、3カ月で10の課題が改善されていくことになります。そのようにして改善を積み重ねることで、お客様が安心して口にできるサプリメントが提供していけると考えます。」
リニューアルした工場見学 自分の眼で安全性を確認
三島工場では7月24日から一般向けの工場見学通路をリニューアルオープンする。リニューアルのポイントは、オリジナルキャラクター「タンクリーン」やサプリメントをモチーフとした造形物が見学ルートの各所に設置されたこと。そして、ファンケルのこだわりでもある「体内効率設計」を視覚的に体験できるコーナーが設置されたこと。今まで以上に親しみやすく分かりやすい工場見学になった。
特に、打錠機でバルクを作る仕組みが学べたり、実際にバルクが高速で作られていく様子が見られるコーナーや、バルクが袋詰めされる充填作業のコーナーは楽しい。それに、高い衛生管理や安全性のもとで製造されていることが分かって安心できる。
工場見学は一般の人でも無料で参加でき、所要時間は約60分。サプリメントがどのように作られているのかを知り、自分の眼で確認できれば、より安心してサプリメントを利用できるに違いない。
※本稿で紹介した工場見学の内容は、報道関係者向けに普段は非公開のエリアも公開している。そのため一般向けの工場見学ルートでは、見ることができない箇所もある。