軽くて強く、腐食しない先端材料といわれている炭素繊維。レーシングカーや飛行機など、軽量化と強度が求められる製品の素材に利用されている。1970年代から工業製品に使われはじめ、東レを筆頭に帝人、三菱ケミカルなど日本のメーカーが技術と品質で世界をリード、国内3社で市場シェアの約7割を占める。特性が極めて高い素材だが、成形加工に時間とコストがかかることが課題とされてきた。しかし、それも研究開発の進捗により乗り越えられようとしている。昨今の炭素繊維事情について、東レの担当者に聞いた。
鉄よりも強くアルミよりも軽い
カーボンファイバーとも呼ばれる炭素繊維は鉄やアルミニウムに比べて10倍近い強度を持ち高剛性、かつ、非常に軽い。「比重」(物質の重量比)で比較すると、鉄:7.8、アルミ:2.7、ガラス繊維(グラスファイバー):2.5に対し、炭素繊維は1.8前後と鉄の約4分の1の重さしかない。
炭素繊維は、アクリル(ポリアクリロニトリル)繊維等の有機繊維を段階的に高温にしながら蒸し焼きにして炭素以外の元素を脱離、炭化させ、分子構造の90%~100%近くを炭素にした状態にして作る。結晶構造上はダイヤモンドに近い。
「髪の毛の10分の1の細さの、ダイヤモンドのように非常に硬い糸だとイメージしてもらうとわかりやすいかもしれません。細いとはいっても特殊な工具がなければ切れません。当社は炭素繊維をボビンに巻いた状態や炭素繊維を織ってシート状にした製品など、用途によってさまざまな形態で販売しています」(東レ担当者、以下同)
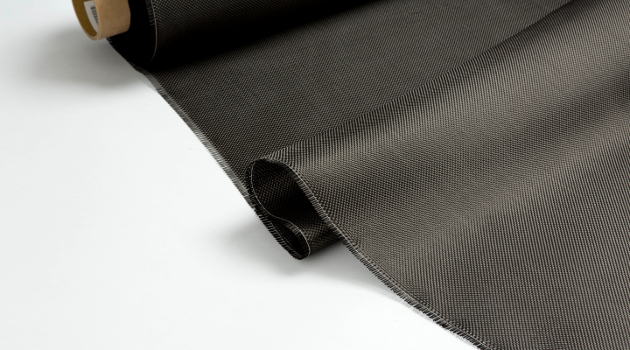
釣竿からロケット、ガスタンクまで 炭素繊維の用途と歴史
ここで少し、炭素繊維の歴史をさかのぼってみよう。
炭素繊維の歴史で最初に登場するのは、かの発明王トーマス・エジソン。19世紀の終わり、エジソンが電球を発明する際に、フィラメントの素材として木綿や竹を焼いたものを使用したのが炭素繊維の始まりだった。しかし、その後フィラメントにタングステンという金属を使用するようになったことで徐々に忘れられていく。
再び炭素繊維が注目されたのは1950年代。高い耐熱性が求められるロケット噴射口の材料として、アメリカを中心に研究が活発になる。国内では、1961年に大阪工業技術試験所(現・国立研究開発法人 産業技術総合研究所 関西センター)の進藤昭男博士 が炭素繊維の製造に関する論文を発表。高性能炭素繊維の時代が本格的に幕を開け、1967年にはイギリスのロールス・ロイス社がジェットエンジンへのCFRPの採用を検討するなど、ロケット・航空機分野での炭素繊維が活用されはじめる。
「東レでもアクリル繊維で炭素繊維を作る研究を、1960年代後半から行っていました。1971年には高強度炭素繊維『トレカ® T300』の製造・販売を開始。当時の世界最大の生産能力の12トン/年を誇りました」
アメリカやヨーロッパの企業に交じって、東レをはじめ東邦レーヨン(現・帝人)や三菱レーヨン(現・三菱ケミカル)など日本企業も炭素繊維業界で先頭グループを形成。1990年までに、採算が合わないとして欧米の各社が炭素繊維の製造から撤退するなか、日本のメーカーはその存在感を増していく。
「炭素繊維の用途が見つからず欧米各社が苦戦するなか、東レは1971年に鮎釣の竿、1973年にゴルフクラブのシャフトへ採用されるなど、まずはスポーツ用途から用途開拓を始めました。趣味の世界は高価で高品質なものが受け入れられるため、炭素繊維を量産しながら、より高度な技術開発や新たな用途開拓を行うのに向いていたのです。
例えば、用心深い鮎を釣るには10メートル以上の長さの竿がいるのですが、当然折れない強度も必要。すると必然的に重くなりますが、炭素繊維を使えば、軽くて丈夫な竿ができます。また、斜めに巻くなど工夫すれば、釣竿に欠かせない『しなり』も出すことができます」
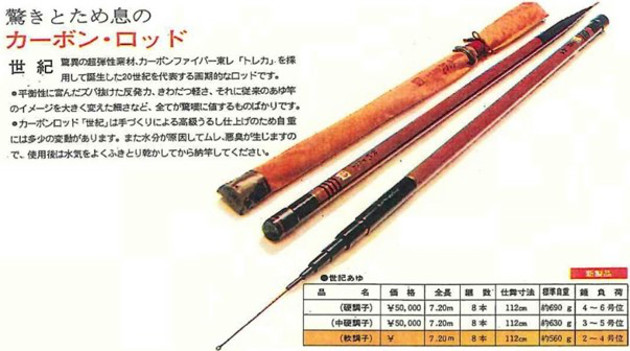
1980・90年代には、欧州のエアバス機や米ボーイング機の尾翼などの一次構造体にも使われ、2000年前後にはガスタンクや船舶などの産業用途も本格化。近年は、風力発電のブレードの骨組みにも炭素繊維が使われている。炭素繊維は他素材に比べて軽いためにブレードの大型化が可能である。また、製造方法によって剛性(硬さ)の調整もできるため、“しなり”を必要としない風力発電の大型ブレードに最適な素材であった。こうした完成品の用途に合わせて特性の活かし方をコントロールできるのも炭素繊維のメリットといえる。
炭素繊維に求められる2つの品質「強度」と「弾性率」
炭素繊維の品質を測る際に指標とされる数値が「強度(ストランド強度)」と「弾性率」だ。「強度」は“折れにくさ”を示し、「弾性率」は「剛性」と同義で“変形しにくさ”を示す。「強度」と「弾性率」はトレードオフの関係にあり、「強度」を上げるほどもろくなり、折れやすくなる。折れにくくするには「強度」を抑えて「弾性率」を高めなければならないが、「強度」が低くなれば、衝撃を受けたときに変形しやすくなってしまう。炭素繊維の開発の方向性は、高強度と高弾性率を両立させる方向性に向かっており、東レでは日々品質向上に向けた研究が行なわれている。
炭素繊維の歴史はチャレンジの歴史
ところで、CFRPという言葉を耳にしたことはあるだろうか? 「Carbon Fiber Reinforced Plastics」の略で、日本語では「炭素繊維強化プラスチック」と表記される。炭素繊維に樹脂を含侵させたシート状の「プリグレグ」を型に合わせて賦形・積層して硬化させたものがCFRP製品だ。
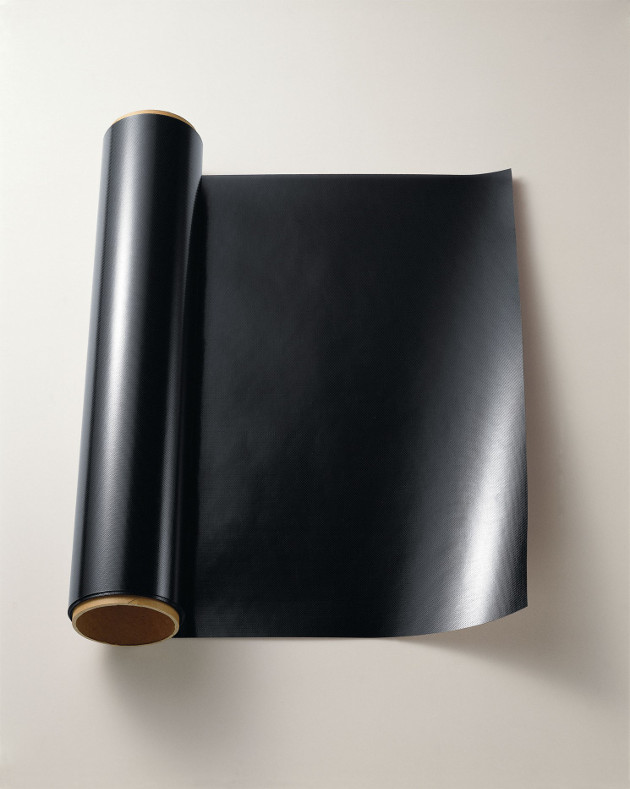
「CFRP製品を樹脂製品と認識している人も多いようですが、炭素繊維にプラスチック材料を含浸した炭素繊維強化プラスチック(CFRP)を用い、焼いて硬化させて成形した複合材部品のことです。製法にいくつか種類があるのですが、軽くて硬い炭素繊維の長所を最も引き出すのがオートクレーブ法といわれるものです」
東レの子会社、東レ・カーボンマジックが採用しているオートクレーブ法は、石膏や金属などで作った型にプリグレグを積層し、それを専用の機械を使って高温高圧下で成形する製法。炭素繊維の性能を最大限引き出せるが、一枚一枚手作業で貼り付けていくため、手間がかかる。そのため、レーシングカーや航空機などの高性能を求める分野には適しても、量産化が必要な一般製品には採用されにくいという面がある。
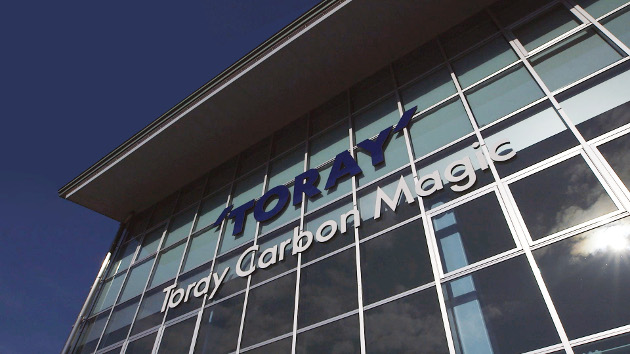
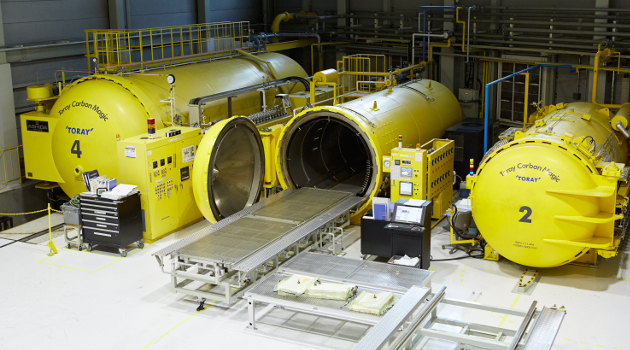
「炭素繊維の歴史は、品質の追求とともに、量産化へのチャレンジの歴史でもあります。オートクレーブ法での量産化は不可能という声もありますが、東レグループでは、オートクレーブ法で製品を開発する一方で、量産化の方法も研究しています」
CFRP部品の用途として最も期待されているのが自動車分野だ。1979年にF1カーに採用されて以来、レーシングカーの分野で積極的に使われてきた。「スーパーGT」など日本国内のレースで今も東レ製プリプレグが採用されている。
市販車でもCFRPを使ったものがあり、フェラーリ・カリフォルニアやマクラーレン MP4-12Cなどのスーパースポーツカーで採用されているが、これらのクルマは生産台数が極めて少ない。BMV i8などのスポーツカーを中心に、より低価格のクルマでも炭素繊維を活用する動きは進み、最近ではBMW i3(2013年11月欧州発売、EV)のようなコンパクトカーにも採用されはじめている。
高級車だけでなく今後、一般車にも普及させるためには、量産化技術が避けて通れない。そのため、東レではオートクレーブ法以外での成形も視野に入れて研究・開発を進めている。
「炭素繊維を使ったCFRPが軽くて強いハイクオリティな素材であることは、各自動車メーカーもわかっています。事実、強度を高めたい特定の部品にだけCFRPを活用するなど、部分的に使いはじめています。CFRPのメーカーも自動車にCFRPを使うための問題解決に向けて研究を進め、金属との共存の道を模索しています」
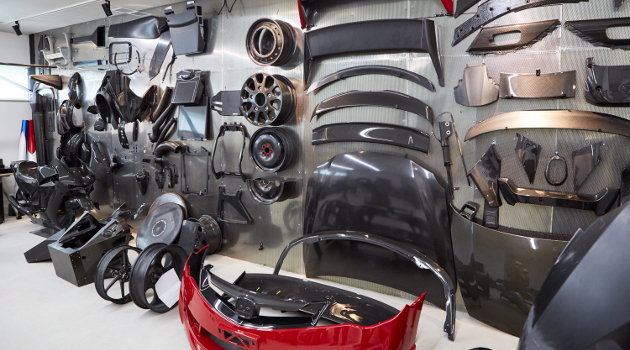
自動車分野での採用拡大に期待! 熱可塑性樹脂の可能性
量産化に向け注目されているのが、CFRPを作る際に含侵させる樹脂の違い。樹脂には「熱硬化性樹脂」と「熱可塑(ねつかそ)性樹脂」の2種類がある。
熱硬化性樹脂はオートクレーブ法でも使われている樹脂で、一旦熱を加えて固めてしまうと、再加熱しても軟化しない。一方の熱可塑性樹脂は、加工後に再び熱を加えると軟化する性質を持っている。しかも、熱硬化性樹脂で作るよりも早く乾き、汎用性が高い。こういった性質を持つ熱可塑性樹脂がCFRP部品の量産化の鍵を握ると見る向きもある。
「一般市販車のように、製造コストに制限があり、CFRPにスポーツカーで使用するような高性能を求められない場合は、コストと性能のバランスを取り、強度は少し落ちますが熱可塑性樹脂の方が採用しやすいのでは、という流れになっています。東レは長らく熱硬化性樹脂でやってきましたが、今後を見据えて2018年7月に、熱可塑性樹脂の技術を持つオランダのメーカーを1230億円で買収しました」
買収金額1230億円は、東レのM&Aの歴史では最大の金額。それだけ東レは熱可塑性樹脂を使ったCRFPに可能性を感じている。
エネルギー問題の解決も視野に!炭素繊維を活用したライフサイクルアセスメント
航空機やクルマ・バイクなど、駆動する機械を軽量化することができる炭素繊維はエネルギーとのかかわりが深い。
「電気自動車が増えれば電気がたくさん必要になります。もし風力発電が広まれば炭素繊維の出番ですし、電力を増やすだけでなく、エネルギー効率を考えて軽量化で消費電力を減らすことも、重要なエネルギー戦略になります。
ライフサイクルアセスメントで考えたとき、炭素繊維を使ってエネルギーを作り出した方がコストもかかりません。現代は、作るときから、使うとき、捨てるときまで考える時代。炭素繊維を効率的な素材として、業界全体で認知を広める活動をしていかなければなりません」
事業化はまだされていないが、炭素繊維の今後の本格普及に向け、経産省の補助事業やNEDO(国立研究開発法人新エネルギー・産業技術総合開発機構)の「戦略的省エネルギー技術革新プログラム」の一環として、CFRPや炭素繊維をリサイクルする取り組みも進められている。
現在の炭素繊維の生産量は、業界全体で年間8万トンだという。それでもここ数年は、年10%のペースで伸びている。量産化に成功すれば一般車にも採用され、生産量は飛躍的に伸びるだろう。炭素繊維が身近な素材となる日も近いかもしれない。
まさかりかついだ金太郎
炭素繊維ってすっげ〜や!
2022.1.28 11:54