アルミニウムよりも軽く、鉄よりも強い素材、CF(炭素繊維)は、航空機やレースカーなど軽量化を求められる乗り物や、しなやかさと強度の両立が求められるゴルフクラブ、釣り竿といった製品に活用されている。鉄に比べて疲労耐性が高く、錆びない、電気伝導性やX線透過率があるなどの機能的特長があり、次世代の先端材料として注目されている。炭素繊維複合材料を使ったコンポジット製品を手掛ける東レの子会社、東レ・カーボンマジックは、CFRPを使って、さまざまな高性能製品を生み出している。レーシングカーの設計・製作を行う童夢カーボンマジックが前身で、現在は大規模な工場を持つ業界屈指の企業となっている。本社工場のある滋賀県米原市を訪ねた。
炭素繊維と樹脂で作るCFRP製品を開発・生産
滋賀県米原市。日本のほぼ真ん中に位置し、メーカーの物流拠点として倉庫も数多くある地に東レ・カーボンマジック(TCM)の開発拠点はある。同社のエントランスには、TCMが過去に手掛けたレースカーやソーラーカー、モーターサイクルなどが展示されている。
TCMは、レーシングカーの開発・製造を手掛けてきた前身の童夢カーボンマジックの時代を含め、長きにわたってレーシングマシンを作ってきた。レースという極限のスピードを競う世界では、軽量化が欠かせない。しかし、同時にアクシデントがあった際にドライバーの命を守る強度も要求される。その2つを兼ね備えた材料がCFRP(炭素繊維複合材料)であり、TCMはその研究・開発から設計、試作・改良、検査、量産までの製造工程を一貫して手掛ける専門家として業界から高い評価を得てきた。
CFRP(Carbon Fiber Reinforced Plastics)
炭素繊維複合材。炭素繊維強化プラスチックとも呼ばれる。ほぼ炭素のみでできた炭素繊維で織ったクロスに、樹脂を含浸させた素材(プリプレグ)を、型に合わせて賦形・積層して硬化させたもの。軽量で高強度、高剛性といった特長がある。
CFRP製品の作り方には、オートクレーブ、RTM、プレスなどいくつかの製法があり、TCMは「オートクレーブ法」を採用。何層にも重ねたプリプレグを高温・高圧化で硬化させる方法で、この製法がCFRPの性能を最も高めるという。
勘と経験がものを言う職人の世界「オートクレーブ法」
オートクレーブ法で作るCFRP製品は「カーボンコンポジット」とも呼ばれ、高い技術と手間を必要とするため、量産品よりも特注品のように生産数の少ない製品がメインとなる。TCMでは、オーダーを受けると、まずはクライアントの要望に沿って、性能・機能・品質などの目標を達成する具体的な開発仕様・開発展開を計画する。
では、製造工程に沿ってカーボンコンポジット製品が完成するまでを見ていこう。
CFRPは設計自由度が高い半面、力のかかる向きや必要な強度を得るためにプリプレグを何層にするかなど、考慮すべき要素が多い。TCMでは、複合材料に特化したシミュレーション技術を駆使し、炭素繊維が最も有効的に作用する最適な構造案を設計。
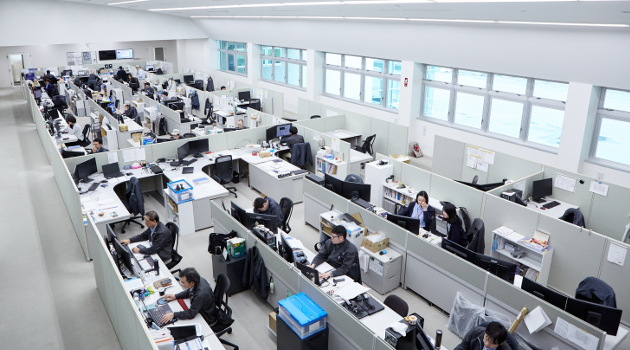
設計が終わると、製造工程に入る。石膏・CFRP・金属などで成形用の型を作り、そこに手作業でプリプレグを貼り付けていく。最先端素材を使った製品の製造にしてはアナログな方法だが、設計書を頼りに一枚一枚丁寧に貼り付ける作業は、誰でもできそうに見えて、実は勘と経験がものを言う職人の世界。プリグレグを貼る方向など、失敗が許されない繊細な工程なのだ。この工程を終えた製品は、パックされて中の空気が抜かれ真空状態にされる。
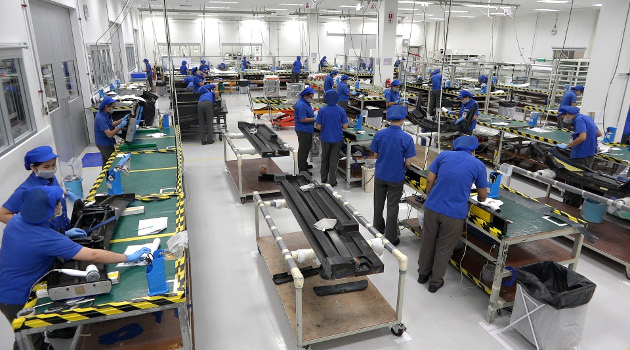
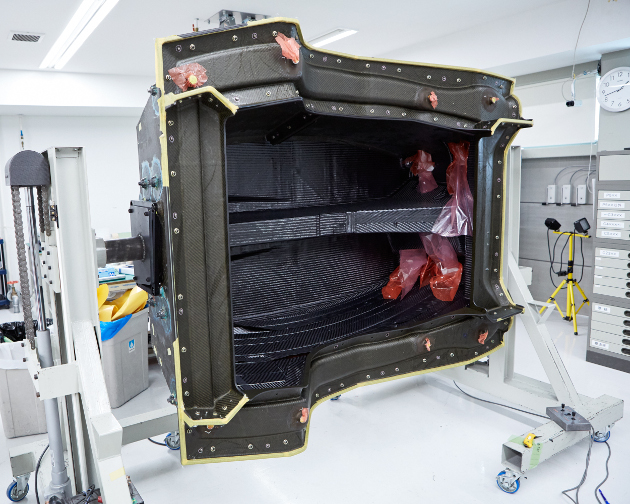
高い品質を担保する加工技術と検査
積層が終わったらいよいよ硬化させる工程。オートクレーブに入れて、高温、高圧下で樹脂を硬化反応させる。この工程でカーボンコンポジット特有の強度を獲得。
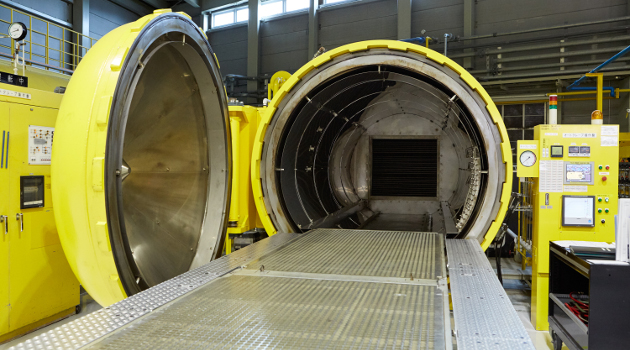
オートクレーブで硬化された製品は型から外され、トリミングしたり穴あけしたり切削したりと、2次加工が施される。カーボンコンポジットは強度が高いため、切ったり穴をあけたりするのにも専用の工具や機械が必要で、TCMは最新鋭のウォータージェットやマシニングセンターなど高性能な機械を導入している。
2次加工を終えた成形品は、ほかの成形品や金属部品と組み合わせて製品となる。CFRPの製品は、部材間の接合技術がとても重要。金属のように溶接ができないため、接着剤で接合する場合が多い。条件に合わせた接着剤の選定や接着手法など積み重ねたノウハウが貴重となっている。
組立が完了すると、塗装などの表面処理を経て製品は完成。外観検査や最新機器による形状計測、X線や超音波による非破壊検査を行い製品はクライアントの元へ届けられる。
TCMは品質検査でも、ISO 9001のみならず、航空業界の品質管理要求であるJIS Q9100やNadcapを取得し、ボーイング社のサプライヤー認定も受けている。航空機の製造はその過程をすべて追えるようにしなければならず、TCMには、ボーイング社の製品を専用に取り扱うスペースも用意されている。
カーボンコンポジットの特性を生かした製品の数々
こうして製造されたカーボンコンポジット製品は、どのようなパーツに使用されているだろうか。
例えば、消防車キャビンの屋根を高くする「ハイルーフキャブ」にカーボンコンポジットを使用し、鉄製から約70%の軽量化と低重心化がなされた。その分、より多くの装備を積むことができるようになった。導入例:「Red Armor」(モリタ)。
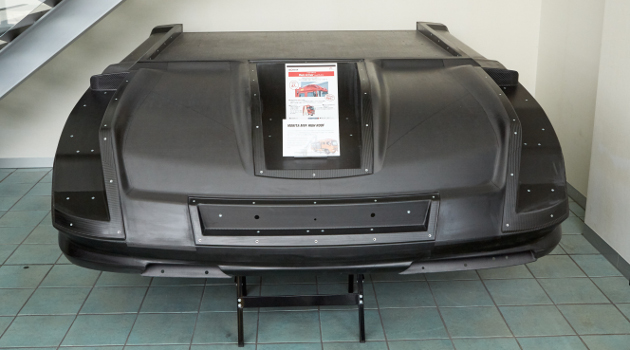
また、ホンダ、トヨタ、日産が参戦している国内最高峰のカーレース「スーパーGT」に参戦するレーシングカーのモノコックは、すべてTCMが作るカーボンコンポジット製。燃料タンクが助手席にあり、レースで事故が起こった際にドライバーを守る車体の基礎に採用されていることからも、カーボンコンポジットの強度と安全性が信頼されている証といえよう。
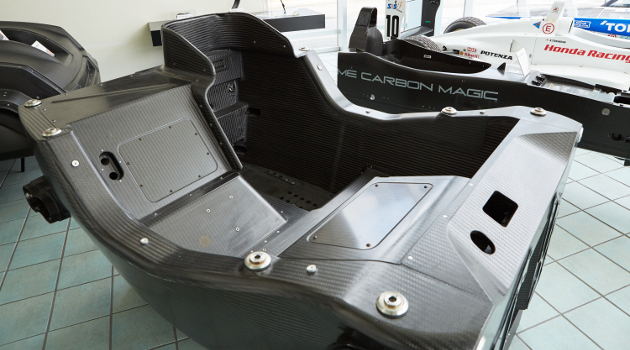
そのほかにも、軽量で強度の高い特長を生かし、飛行機・新幹線のシートや、競技用の車いす、アタッシェケース、楽器ケース、サングラスなどにも使用されている。カーボンコンポジットのしなやかさや反発力を求めて製作された競技用の義足などもある。また、最近は織り目の美しいデザイン性も注目され、炭素繊維織物の柄を生かした名刺入れや時計なども登場している。
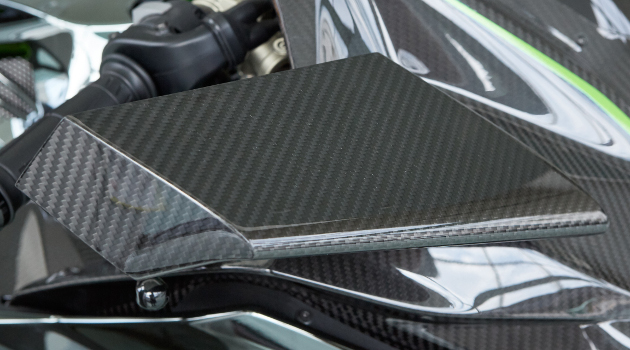
東レ・カーボンマジック代表取締役社長・奥明栄氏に聞く【カーボンコンポジットの未来】
東レ・カーボンマジックの前身である童夢カーボンマジックは、レーシングカーコンストラクターの童夢がレース活動の中で培ったカーボンコンポジットの技術を転用するため、2001年に設立された会社。設立時から同社を率いる代表取締役社長・奥明栄氏に、その歴史やカーボンコンポジットの将来性について話を伺った。
童夢からどのようにして東レ・カーボンマジックを設立することになったのですか?
童夢は1970年代からレース用の車やバイクを開発・製造する会社として活躍してきました。私自身、機械工学を学んでいた学生時代から童夢の活動に参加し、そのままレーシングカー設計を仕事にしました。
レーシングカーを速くするには、空力やエンジン性能などさまざまな要素がありますが「軽量化」もその一つ。1983年に初めて炭素繊維に接し、レーシングカーを作る素材に最適だと着目。その後、研究を重ねてレースで使いながらノウハウをため、カーボンコンポジットの高い技術を身に付けたことで、レース以外の分野から声がかかるようになったのが、童夢カーボンマジックの設立につながりました。レースでのノウハウを社会に生かしたいという思いが根底に流れています。
そのうちに、カーボンコンポジットの用途が広まり、2010年ごろには今後の急激な需要拡大が予想されました。2005年にタイに量産のための工場を設立するなど、童夢カーボンマジックでも準備を進めていましたが、その拡大する需要は童夢カーボンマジックだけでは対応しきれない規模になると考え、炭素繊維世界ナンバーワンの東レグループの一員として共に進んでいく道を選択しました。
当社の技術力に目を付けて、異業種も含めあちこちから引き合いの声はありましたが、高性能のカーボンコンポジットで社会貢献したいという設立の志を共有できるのが東レでした。1983年に最初に触った炭素繊維も東レ製でしたから、運命的なものも感じます。素材メーカーである東レにとっても、開発・設計・製造に注力していく出口戦略を考えており、両社の方向性が合致したのも要因です。
炭素繊維とはどのように出合ったのですか?
1982年に初めてカーボンコンポジットを触りました。それまではレーシングカーのフレームは鉄かアルミニウム製、ボディはグラスファイバー製が一般的でしたが、ルマンなど時速350kmで走る世界では、そのような車体は1レース終わるころにはボロボロになっています。
ヨーロッパではF1を中心に炭素繊維という新素材がレーシングカーの設計・開発に使われているという話は伝え聞いていました。しかも、その炭素繊維は日本製だという。それなら何とか手に入らないかと画策し、知り合いの伝手で炭素繊維を入手して、グラスファイバーの代わりに使ってみたところ、軽くて強い素材で、レーシングカーを速くするには最適な素材だと直感しました。
グラスファイバーの代わりに車体に使うだけではなく、F1のようにフレームにも使いたかった。しかし、当時は教本もなく、どう設計し、どう作るのかまったくわからない。そこで、ある重工メーカーで複合材を研究している方に協力してもらい、海外の資料や情報を入手、試行錯誤の末、1985年にフルカーボンコンポジット製の鈴鹿8時間耐久レース用のバイクを作りました。
設計から製造まですべて自分たちでやりましたね。1986年から自動車レースのフレームも作り始めましたが、常に手探り状態で開発を進めていました。そうこうして、10年後の1995年にはレーシングカー開発に要するカーボンコンポジットの技術を完全に身に付けました。
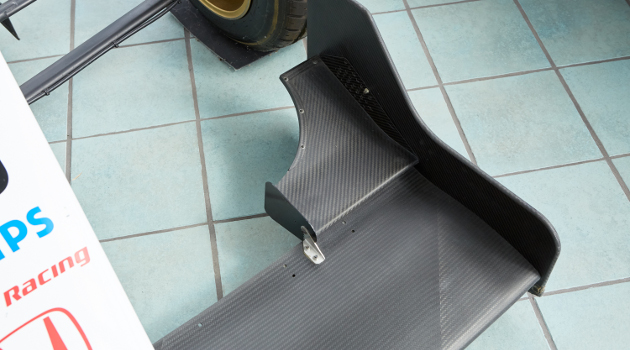
TCMの強みは何でしょうか?
短期間でクライアントが求めている製品を作り上げる、量産や品質保証まで一貫して自社で行う体制です。カーボンコンポジット製品を作るのに重要な、設計や解析のフェーズを専門に担当する部隊がおり、また、タイには量産工場があります。米原の本社をヘッドクオーターに、それぞれの製品に合わせた最適な生産体制が構築できます。
また、設計を手掛けるエンジニアも優秀な人材が揃っています。ただ設計するだけでなく、炭素繊維の特性を理解した上で設計するには、炭素繊維の知識や経験も必要となってくるため、当社では独自にエンジニアを育成しています。
全体のマスが大きくなり、レーシングカーの設計・開発の仕事の割合は減っていますが、当社の原点でもあるレーシングカーの製造は止めてはいけないと思っています。“当社のアイデンティティ”という抽象的な意味合いだけでなく、レースカーの開発はエンジニアの育成に欠かせません。レースの世界では極限の戦いが繰り広げられ、そこで経験を積むことで独創的なエンジニアが生まれるのです。
日本にはカーボンコンポジットを扱えるエンジニアが少ないのが実情です。レーシングカーの本場ヨーロッパでは、その技術をスーパーカーに応用し、それを高級車、一般車と落とし込んでカーボンコンポジットを広めています。一方、日本ではカーボンコンポジット適用の対象をいきなり量産車でと考えたために、手間がかかる「オートクレーブ法」は最初から考慮されず「アウト・オブ・オートクレーブ」が合言葉の時期もありました(笑)。
しかし、カーボンコンポジットの性能を最大限に引き出すには、オートクレーブ法が最適です。オートクレーブ法は手間がかかるし、大きな装置も用意しなければならないなど、マイナス面を指摘する声もありますが、カーボンファイバーは高性能だからこそ価値があります。性能を犠牲にしてコストダウンするのは、もうちょっと先、カーボンコンポジットの突出した効能がしっかり認知されてからでよいと思います。
TCMは今後、どのような道に進みますか?
カーボンコンポジットの需要は拡大しています。当社も件数、生産量ともに右肩上がりの成長を続けています。しかし、今後も成長を持続させるためには、高性能なカーボンコンポジットを量産する体制を強化しなければいけません。
オートクレーブ法を維持しながらも、機械化を含めた製法の進化・改良にも取り組んでいきます。プリグレグを張り付ける「積層」の前後の工程は、現在でもかなりオートメーション化が進んでいます。しかし、積層はデリケートな作業のため、まだまだ人の手が必要。設計段階で工夫するなどして、効率化・機械化を推進していかなければなりません。
そのためには、製品の企画・設計だけでなく、コンセプトワークから参画する必要もあると考えています。例えば、自動車分野では、「ガソリンから電気へ」「エンジンからEVへ」の流れのなか、カーボンコンポジットなら自動車のコンセプト自体を変えることも可能です。
自動車メーカーはこれまでの自動車の延長線で考えますが、EV車はまったく新しいコンセプトになってもいいはずです。カーボンコンポジットを含め、新しいコンセプトの製品を作るのに素材の最適化をクライアントと一緒に考えることで、カーボンコンポジットを広めていきたいと思っています。
カーボンコンポジットの可能性を示すプロジェクト
奥社長が語っていたコンセプトワークからの参画は、具体的なプロジェクトとして動き出している。その一つが「しなやかポリマー」を使ったコンセプトカー「ItoP」(Iron to Polymer、アイトップ)だ。
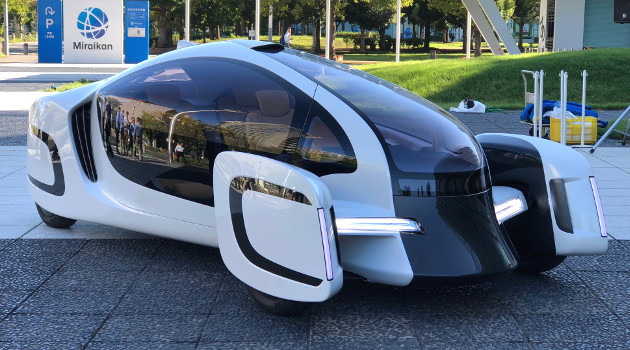
「ItoP」は、新素材「しなやかなタフポリマー」を車体のさまざまな部分に採用した近未来カー。内閣府がメーカーや研究機関と進めている革新的研究開発推進プログラム「ImPACT」の一環で、東京大学・伊藤耕三教授の指揮の下、東レ・住友化学・三菱ケミカル・AGC・ブリヂストンが開発したコンセプトカー。
ポリマーは人類の発明した素材で最も用途が広いともいわれているが、薄くすると壊れやすく、厚く硬くすると脆くなる性質が課題だった。それを解決するのが「しなやかポリマー」で、東レもプリプレグにしなやかポリマーを含侵させて、しなやかさを増したカーボンコンポジットを開発。サスペンションやシートなど、「ItoP」のさまざまな部品として採用されている。「ItoP」の設計・製作はTCMが担当した。
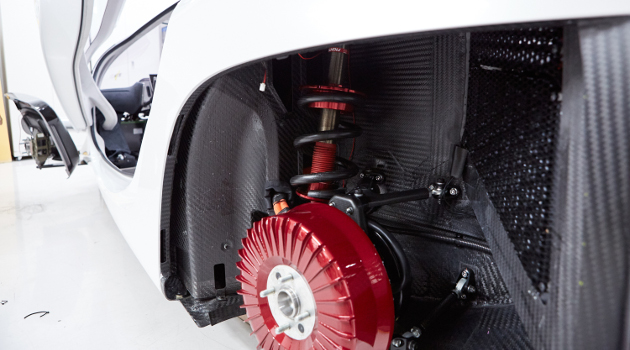
認知度や普及率も含めて、カーボンコンポジットの未来はこれからだ。今後は航空・宇宙、医療、産業用機械・ロボットなど高性能な製品から、市販の自動車やインテリア、スポーツの分野など私たちの生活の身近な製品へと、用途の幅は広がっていきそうだ。