東レが開発した「しなやかでタフなポリマー材料」は、剛性(変形しにくさ)と靭性(粘り強さ)を兼ね備えた革新的なプラスチック材料として注目を集めている。昨今の環境対策を見据え、自動車をはじめとする軽量化が必要とされる分野への応用が期待されるところだ。東レの研究主幹である小林定之さんに話を伺い、同社が開発した新規材料の開発経緯や市場でのポテンシャルに迫った。
エンプラの長年の課題に東レが出した答え
自動車や家電、PCや建築など、身の回りにあるモノの材料の多くに金属とプラスチックが使われている。市場からの高性能化、高機能化の要求を満たすには単一素材では賄いきれないことから、金属材料はその用途によってさまざまな組み合わせの合金が作られており、プラスチックも同様にさまざまな配合の原料が使われている。
例えば自動車の場合、車体重量の多くを金属が占める。金属は衝撃吸収性も高く強靭な材料なため大部分に使われるが、重いのも特徴だ。近年では環境対策を目的とした省エネ化や電動化(EV)によって自動車も軽量化が進められており、その手段には“脱金属”、つまり金属より軽いプラスチックへの代替が挙げられている。
実際に、優れた耐熱性、剛性、強度を有する高機能なエンジニアリングプラスチック(エンプラ)は自動車のエンジンルームの内部品等に使われている。ただ、強化のためにガラス繊維等を組み込むと固くはなるが脆くなって強い衝撃や繰り返しの折り曲げに弱くなることもあり、疲労耐久性の向上は長年の課題とされてきた。そのため自動車の部材としての利用は限定的で大きな軽量化には結びついていないというのが実情だ。
だが、東レが開発した非常に高い物性を有する「しなやかでタフなポリマー材料」(以降、しなやかなタフポリマー)は、金属からプラスチックへの代替を促進する可能性を示す。
金属のような衝撃吸収性を持ったプラスチック
「しなやかなタフポリマー」は、ポリアミド(通称:ナイロン)と呼ばれるエンプラに特殊なポリマー(※)を組み合わせることで金属材料のような衝撃吸収性を持ったプラスチック材料だ。
※ポリマー=プラスチックを構成する高分子化合物
従来のポリアミドは、分子が結合もしくは絡み合う形で“固定された網目構造”をとる。野球場にあるネットのような状態だ。それを両方から引っ張ると網目が伸びきったときに切れて壊れてしまう。一方、「しなやかなタフポリマー」は引っ張りに応じて“網目が変形”するため切れにくい。
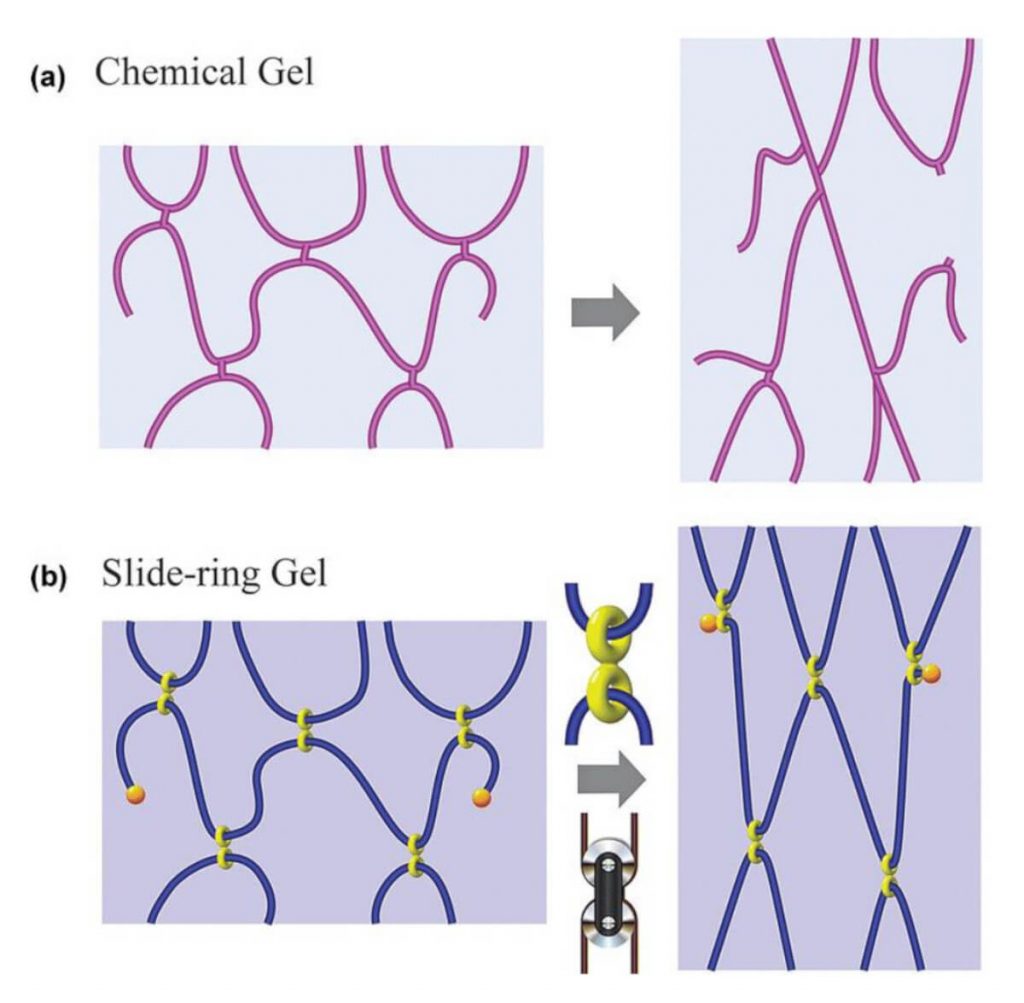
実際、引っ張りに対する強度を比較すると、従来のポリアミドに比べて5倍以上の強度を実現し、耐久性がわかる折り曲げ試験では3万回の折り曲げをものともせず従来の15倍以上の強度が得られたという。また、衝撃吸収性も約4倍と高い物性を示した。
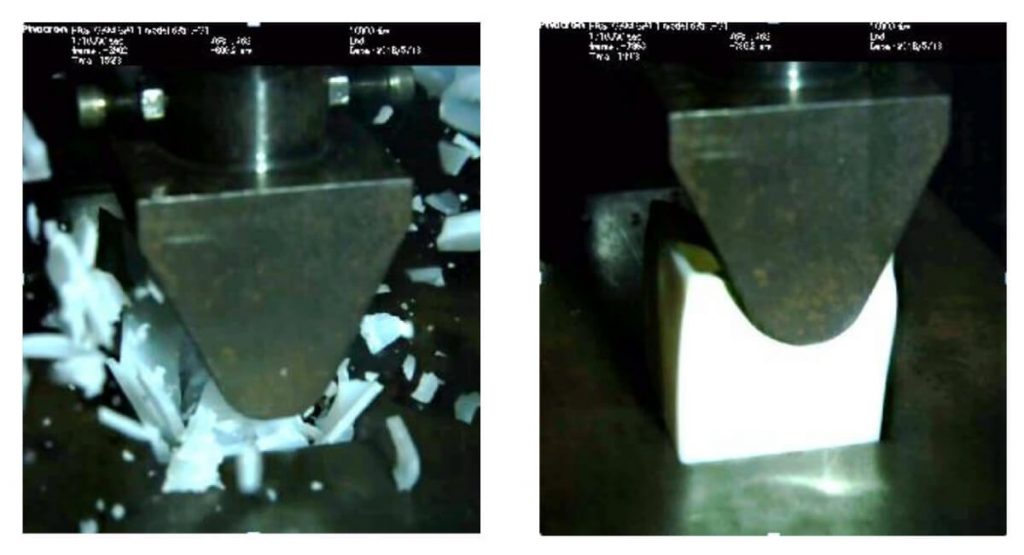
「しなやかなタフポリマー」の特長(対ガラス繊維強化系ポリアミド)
- 引っ張り強度:5倍以上
- 対疲労特性:15倍以上
- 衝撃吸収性:約4倍
ポリアミドの性能をここまで高めたのは、ポリアミドに組み込んだ「ポリロタキサン」と呼ばれるネックレスのような構造のポリマーだ。「環動ポリマー」構造と言い、網目が伸縮することで引っ張りに強い強度を示す。普通、針穴に糸を通すのも難儀だが、分子レベルでこうした構造をとるのは極めて高度な技術を要する。
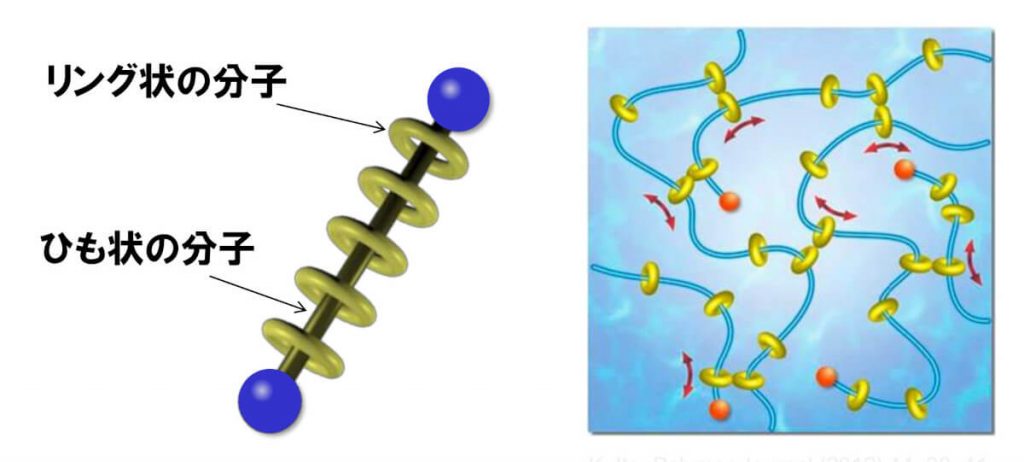
ポリロタキサンはもともと大阪大学の原田 明教授が開発したもので、それを材料レベルのサイズに拡張(ゲル化)したのが東京大学の伊藤耕三教授だ。
東レではかねてよりポリアミドをベースとしたプラスチック材料を自動車向けに供給しており、より強い強度を求めて研究開発を進めていた。そんななか伊藤教授のポリロタキサンに注目した東レは、ポリアミドにポリロタキサンを組み込むことを目指す。
「2014年に、内閣府 総合科学技術・イノベーション会議が主導する革新的研究開発推進プログラム(ImPACT)における伊藤先生の研究プログラムの一環として研究開発が進みました。ポリアミドにポリロタキサンの構造をいかに入れるか、という点が難しいポイントでした」(東レ・小林さん、以下同)
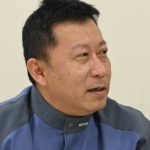
東レ株式会社 化成品研究所・研究主幹/博士(工学)
小林定之 こばやし さだゆき
分子レベルで混ざり合う性質を相溶性(そうようせい)というが、一般的に異なる種類のポリマーを混ぜるのは難しく、単に混ぜるだけでは分離してしまうことがある。東レがポリアミドとポリロタキサンという2つのポリマーを相溶化させることができたのは、複数のポリマーをナノレベルで混ぜ込むことを可能とする独自の「ナノアロイ®」 技術を有していたためだ。
ナノアロイ®
複数のポリマーをナノメートルオーダー(10億分の1メートルの規模)で微分散させることで、従来材料と比較して飛躍的な特性向上を発現させることができる東レ独自の革新的微細構造制御技術。提唱者は小林定之さん。一般的な「ミクロンオーダー(100万分の1メートルの規模)」のアロイ(合金)では実現できなかった高分子材料の高性能化・高機能化を可能にする技術であり、東レのみが基本特許ならびに主要な製造特許、用途特許を保有。
このように「しなやかなタフポリマー」は従来のポリアミドと比べて非常に高い物性を有するため金属材料の代替として期待できるというわけだ。
「しなやかなタフポリマー」で広がるエンプラの可能性
「しなやかなタフポリマー」の応用展開は広い。前述のように自動車部品向けに供給しているガラス繊維強化系ポリアミドとの置き換えをはじめ、剛性と靭性を要する他のプロダクトにおいても金属材料の代替として期待できる。
「自動車で考えると、歩行者の脚部の保護や乗員を保護する衝撃エネルギー吸収パッド等に検討ができます。実際にImPACTで自動車を作った際にも採用されました」
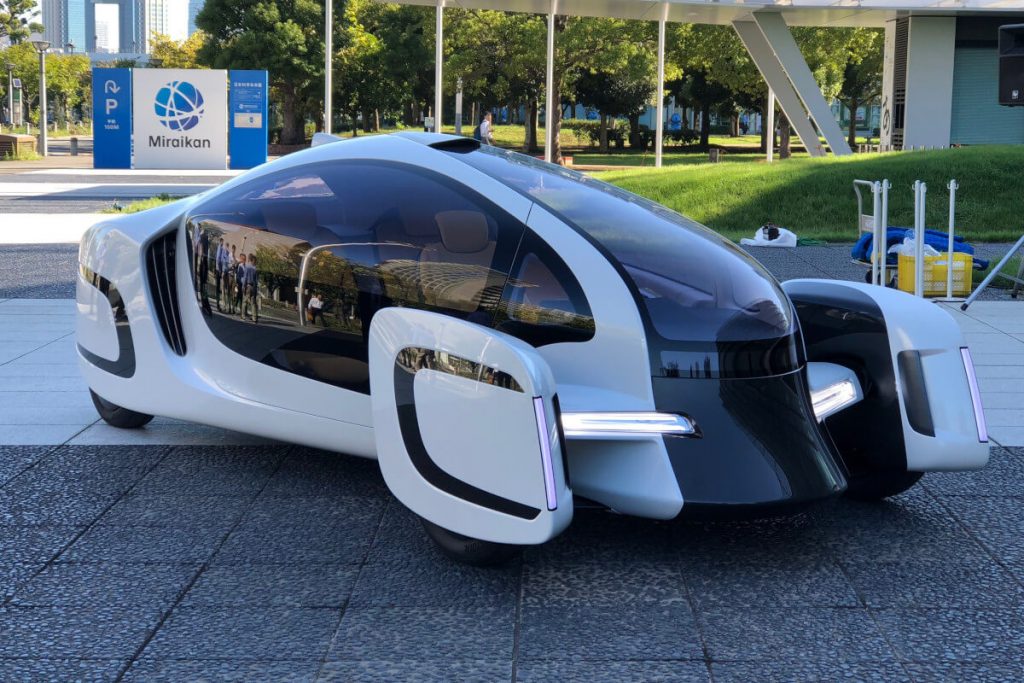
仮に、複数の部材を組み合わせる金属パーツを、一体成型が可能なプラスチックに置き換えることができれば、工数やコストは大きく圧縮されることになる。また、自動車以外にも家電やスポーツ用品などさまざまな分野に応用できるだろう。
しかしながら、すぐに採用されるのは難しいかもしれない。全く新しいタイプの材料は、メーカーの信用を得るまでに時間がかかるからだ。ポリロタキサン自体は、すでにゴムメーカーがゴルフボールの素材として採用した例があり、小林さんもスポーツ用品や家電は近い将来に導入が進むと見ている。しかし、本命の自動車向けでは、さまざまな試験を経て本格的な導入までは2~3年はかかると考えているという。
「しなやかなタフポリマー」発表以降、東レは多くのメーカーからの問い合わせを受けているというが、採用例の多さは新素材の信用につながるため「しなやかなタフポリマー」はしばらく実績作りへの注力が必要だろう。また、ポリロタキサンは現在、伊藤教授が取締役を務める東大発のベンチャーASMが供給しており、供給量が少ないためまだまだ高価。今後、メーカーの採用例が増えていけば低コスト化にもつながるはずだ。
ところで、近年その需要が高まるリサイクル性についてはどうだろうか。
「『しなやかなタフポリマー』は熱可塑性樹脂であるため理論上はリサイクルが可能です」
プラスチックは「熱硬化性樹脂」と「熱可塑性樹脂」に分類される。熱硬化性樹脂は網目がガチガチに固まった構造をしており加熱しても溶けないため、リサイクルはペレット化や粉砕等で他の加工品に混ぜる手法をとる。一方、熱可塑性樹脂は加熱によって溶け、粘性の高い液状になる性質がある。そのため熱可塑性樹脂は廃棄後に再び溶かして成形することができリサイクルが容易だ。採算がとれるかどうかはやはり市場における普及量がネックとなるだろう。
繊維の東レがプラスチック材料を作る理由
東レは創業当初、化学繊維レーヨンのメーカーとして設立され、その後、繊維で蓄積した技術を基にプラスチック材料などの事業を多角化してきた。現在はフィルム、ケミカル、樹脂、電子情報材料、炭素繊維複合材(CFRP)、医薬・医療、水処理・環境といった幅広い分野で先端素材を開発している。
ポリマーを固形状にすればプラスチック材料となり、引き延ばして固めれば繊維となる。そういう点では繊維とプラスチック材料は共通しており、東レ=エンプラという印象が実態に合っているかもしれない。実際に決算資料を見ると売上高に占める割合は繊維が38%、プラスチックやフィルムなどの機能化成品が38%を占める。また、近年ますます需要が高まるCFRPの製造も行っており、今後も先端素材メーカーとして躍進していくことだろう。